In 2019, over 21 million square feet of outpatient facilities were built in the U.S., driven by the current healthcare trends of reducing operating costs, improving access to care and enhancing the patient experience.
While outpatient facilities are less expensive to build and operate than a traditional hospital and are often situated in suburban locations where real estate is more affordable, there are still significant cost factors that can easily tip the scales on your bottom line.
How does Consigli—which has built 40+ outpatient care centers—collaborate with owner and design teams to deliver high-quality, durable buildings in an efficient, cost-sensitive manner? Brian Hamilton, Consigli’s Director of Healthcare & Life Sciences, provides 3 Critical Insights to Consider When Planning Your Next Outpatient Facility.
Certainty of Cost
On any project, healthcare owners are looking for one thing—certainty. Certainty of first cost, first patient date and the long-term operational efficiency of the building they’re investing in.
Target Value Design (TVD) is one of the best ways to control costs and get early budget certainty. It directs a design and construction management team toward a budget—not a blank check—by providing cost buckets for various building elements (i.e. building enclosure, M/E/P, finishes, etc.) that drive the cost of outpatient facilities. If costs need to be moved from one bucket to another, the value and impacts of that move need to be considered.
Consigli Tip: As a rule of thumb, outpatient care facility budgets typically follow a 30/30/40 rule: 30% on finishes, 30% on the building envelope and 40% on M/E/P systems. Traditionally, outpatient facilities have been significant consumers of energy due to the specialty equipment, lighting and HVAC controls (i.e. air exchange) required in the spaces. If you can gain efficiencies in the M/E/Ps, there can be significant long-term cost savings as a result (more on this later).
Leveraging Buying Power
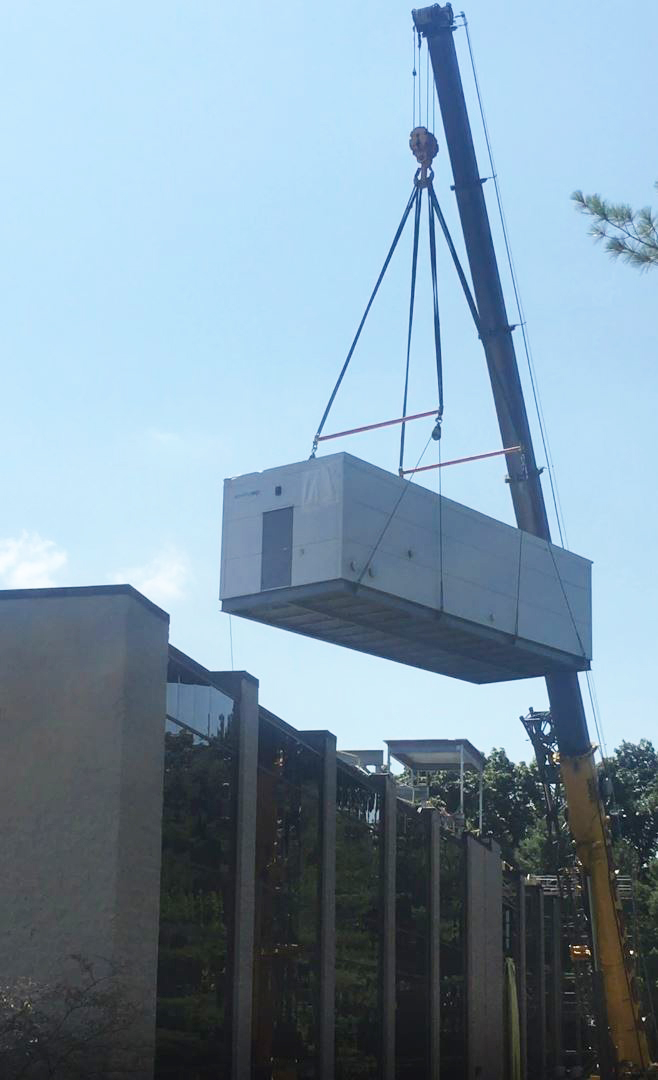
Pre-fabricated mechanical penthouse at Dana-Farber Cancer Institute’s Merrimack Valley Cancer Center
Standardization of building systems and finishes over a multi-facility rollout will result in a cost savings and long-term ease of maintenance. When things like HVAC, heating, elevators, finishes, flooring, ceilings, generators and façade systems are uniform across multiple sites, there are opportunities that become available that can improve cost, schedule and long-term maintenance for the facilities.
Consigli Tip: There are three strategies that we’ve seen consistently lower costs by standardizing building design across multiple sites: (1) Designing for Pre-fabrication, (2) Opening Up the Competition and (3) Bulk Buying Through Standardization. Smart owners will push design and construction teams to creatively employ one, two or all three of these strategies on their projects:
- Designing for Pre-fabrication: Pre-fabrication is a proven strategy to accelerate schedules and reduce costs, while removing labor from the jobsite and assembling building components in a controlled, off-site environment. When cost certainty and speed are driving factors in a project—particularly a project that features repetitive elements like exam rooms—pre-fabrication should be a major topic of conversation.
- Opening Up the Competition: When building off-site from your primary hospital campus, the door is opened to utilize different vendors (i.e. elevators and building controls) than those embedded in the hospital itself, which can lead to more competitive pricing.
- Bulk Buying Through Standardization: By purchasing materials in greater quantities, there is an inherent cost savings. This approach also mitigates escalation in multi-building facility rollout that can span several years. Furthermore, your facilities staff will thank you because maintenance becomes easier and more predictable (i.e. attic stock is the same for all facilities).
The Right Site
On any ROI-driven project, site selection is a major deliberation and outpatient care facilities are no different. New construction typically presents a higher acquisition, development and construction cost, but lower existing building conditions risk. Renovations, on the other hand, can require months of enabling work and costs up to $50/SF before the building is even fit-out ready. Both scenarios come with their own set of advantages and risks that need to be thoroughly evaluated.
(L) Former grocery store transformed into Caremount Medical’s Rhinebeck, NY location (R) Kingston, NY Macy’s department store repurposed into a modern multi-provider outpatient facility
The trend of capitalizing on the increased vacancy of malls and shopping centers has presented opportunities for convenient, accessible care closer to where patients live—and more cost-effective developments for healthcare organizations. While building systems will likely require upgrades (and probably an outright replacement) and the façade may call for enhancements for energy performance and aesthetics, you’re starting with an existing building and a relatively blank canvas. This is a popular alternative to new outpatient construction and will continue to be for the foreseeable future.
Consigli Tip: Whether you’re building new, renovating or repurposing, site selection can easily tip the scales on what’s feasible and what isn’t. When choosing your site or building, keep in mind these three primary cost drivers: (1) Below-grade Conditions & Infrastructure Availability, (2) Heating & Cooling Method and (3) Sound Transmission.
- Below-grade Conditions & Infrastructure Availability: On new buildings, below-grade conditions (i.e. ledge and hazardous soils) and infrastructure availability are critical considerations. Sites requiring soil abatement, significant earthwork and new utility infrastructure will pinch costs from the beginning, and on building components that won’t enhance patient services.
- Heating & Cooling Method: Remember, mechanical, electrical, plumbing and fire protection systems are going to make up approximately 40% of your budget, so decide early if you’re designing your facility to run more like a hospital or more like an outpatient facility. If it’s a 10-hour per day building, system functionality needs are different than that of a 24/7 hospital environment. As such, systems can be simplified, which also means less steel, less screen wall and therefore, less cost.
- Sound Transmission: Sound transmission is always a major concern when designing and building healthcare facilities, with a justified focus on patient confidentiality and the overall patient experience. Privacy from exam room-to-exam room and corridors-to-exam rooms is a non-negotiable, and there are multiple ways to mitigate noise transfer using different structural elements and building systems, at varying price points. The most common systems include demountable partitions, ducted returns, sound masking and walls-to-deck construction. Consider all four systems and how they can work together—not each individually—to determine the best combination for your facility.
In-House Expertise
Project Executives Charles Canepa and Vincent Fiorillo have experience with all the major hospital systems in the New York Region. If you are planning a renovation or expansion of your outpatient facility in the five boroughs, Long Island, Westchester or New Jersey, Charles and Vincent can assist you to ensure the success of your next project.